Glass CNC working center
Glass type:
Applications:
Features:
- Type: horizontal working center, vertical drilling and milling machine, vertical working center
- Integrate drilling, milling, edging, polishing, and other functions in one
- 12000 RPM high-power high-end electric spindle, long lifetime
- Patented air seal and stator glue injection waterproof technology
- Ultra-high precision and stability
- CAM software automatic system, process program is efficient and reliable
- Simple operation, fully automatic control
- Cool inside the tool and outside the tool, good cooling effect
- Tool path optimization, reducing idle stroke and shortening the processing time
- The beam and bed adopt a new structure, high strength and stability
- New large-capacity tool storage
- No processing interference zone, independent control of the suction cup
- Automatic suction cups can hold any size glass
- Large-size glass processing is stable, minimizing processing vibration
- X, Y, Z-axis move fast
- Automatic tool measuring device
- Tool real-time compensation function, high polishing quality
- High-quality tool materials, higher glass processing quality
- The internal coil of the spindle adopts a fully sealed design
- Highly rigid structure, twice the acceleration
- Highly flat worktable platform to ensure the best processing
- Low wear, the machine still maintains high precision after many years of use
- Minimal mechanical wear and almost maintenance-free
- Glass positioning is convenient and fast, reducing the time by 40%
- Glass support rollers and suction cups suppress vibration during milling
- Various shapes of glass can be processed
- Centralized automatic lubrication oil supply system
- High-precision servo motor drives each axis, digital control system
- High-precision ball screws and linear guides
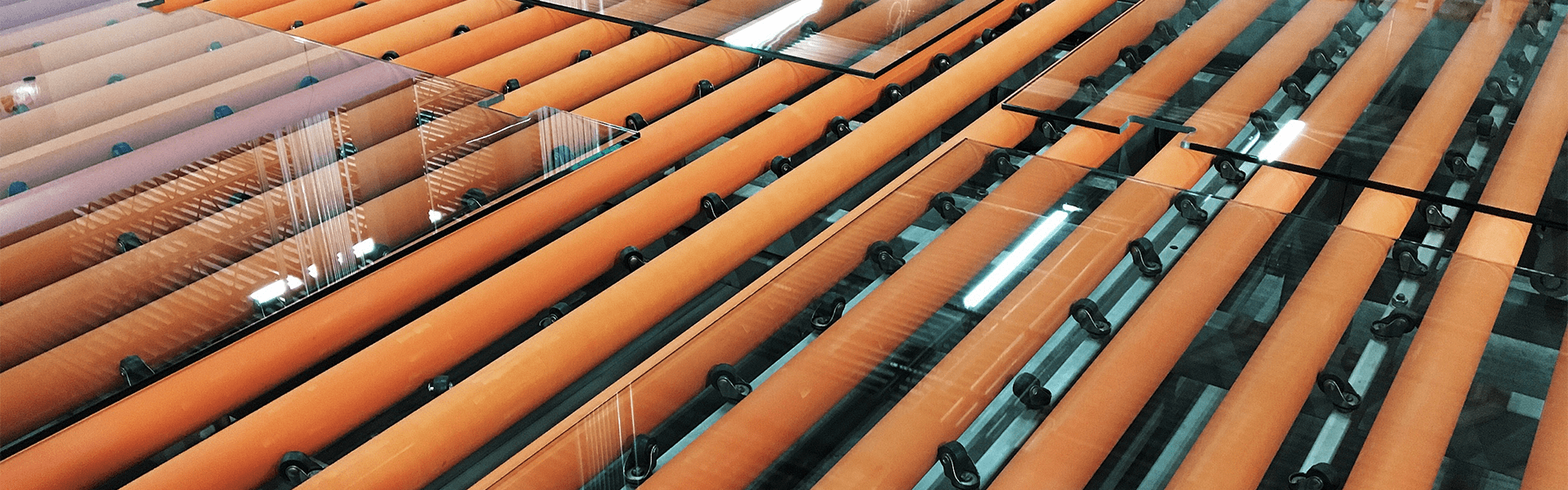
Machine Introduction
Glass CNC working centers are mainly divided into three types: horizontal glass CNC working centers, vertical glass drilling and milling machines, and vertical glass CNC working centers.
The glass CNC working center is suitable for drilling, milling, edging, and polishing flat glass of different thicknesses and sizes. The equipment adopts a computer numerical control system to realize the control of each axis, with very high control accuracy. By generating graphics through CAM/CAD software, complex tasks can be completed in a short time and high-quality glass can be processed.
1. Vertical Drilling and Milling Working Center
This high-end vertical five-axis clamp-type glass working centers are used for glass drilling, milling, chamfering, and internal edging. The equipment has high processing efficiency and processing quality: high-end CNC operating system accurately controls each servo axis; independent research and development of high-power electric spindle; clamp mechanism to fix the glass without damaging the LOW-E film; The processing area is equipped with a set of pressure rollers and supporting wheels to improve the stability of the glass during processing.
Vertical drilling and milling are mainly used in shower door glass, architectural glass (frameless glass doors, glass curtain walls, glass railings), etc.
The main advantages of the equipment are dual-spindle drilling: achieve high-precision and high-quality drilling; the processing of large plates of glass with internal cutouts and special-shaped glass; easy to form a CNC + washing automatic connection with a vertical washing machine; The required floor space is small, glass loading is convenient, especially for the large size glass.
2. Suction Cup Type Vertical Working Center
This series of suction cup type vertical working centers have multiple functions in one machine, which can perform drilling, milling, grinding, polishing, and other processing on the outer and internal of the glass. Independent research and development of high-power electric spindle, the front spindle head with C-axis rotation and auxiliary clamping mechanism, front and rear spindles with intelligent water jackets, to ensure extremely high processing efficiency and quality. The glass is driven and fixed by the suction cup system, and each suction cup is independently controlled to avoid processing interference areas. This ensures there is no damage to the LOW-E film.
The main advantages of the equipment are: grinding or polishing the external and internal of large glass and special-shaped glass; double-headed drills to achieve high-precision and high-quality drilling; it is possible to connect with a vertical washing machine.
3. Horizontal Three-Axis CNC Working Center
The horizontal three-axis CNC working center can perform drilling, milling, grinding, polishing, and other processing on the external and internal of regular shape glass and special-shaped glass. The positioning columns are used to position the glass, and the glass is fixed by the suction cup after positioning, and then the processing is performed. The system has the function of real-time polishing compensation to ensure high-quality polishing.
4. Horizontal Four-Axis CNC Working Center
The horizontal four-axis CNC working center adds the C-axis rotation function of the spindle based on the horizontal three-axis working center and is equipped with a right-angle machining head. It can not only process the internal and external of shaped glass, but also use the right angle machining head to connect the bowl wheel to process the outer of the ultra-thick large glass. The efficiency is more than 3 times than using a regular milling tool.
5. Horizontal Five-Axis CNC Working Center
The horizontal five-axis working center is equipped with a self-developed AC-axis double-angle electric spindle, with three linear motion axes X, Y, and Z and two rotary motion axes A and C, and can realize any four-axis linkage. In addition to all the functions of the horizontal three-axis and horizontal four-axis working center, it also has special processing functions such as processing irregular bevels and engraving.