Shaped Bending Glass Tempering Furnace
Glass type:
Applications:
Features:
- Various special-shaped (single-curved, double-curved, multi-curved) curved tempered glass
- Unequal arc, gradual arc, special-shaped bend, multi-curvature automatic arc adjustment
- Suitable for a variety of glass types, high-quality tempering, no pressure marks, no deformation, no pitting, and optical performance is guaranteed
- The arc-changing mechanism adopts a precise hydraulic and servo system, and high-quality profiles ensure accurate glass shapes and high arc forming accuracy
- The arc-changing system is stable and reliable, ensuring product arc/radius repeatability and high consistency
- The intelligent heating control algorithm, QX intelligent digital control system
- Quartz ceramic rollers with perfect straightness, roundness, and thermal deformation, without SO2
- Combination of multiple tempering processes to eliminate glass defects, edge deformation, white marks, roller marks, etc.
- Products comply with ANSI Z97.1, EN 12150-1:2000, GB15763.2-2005, GB/T9963, GB/T9656, JIS R 3206, and other tempered standards
- Flexible heating chamber design, multi-station configuration options, greatly increase output
- General-purpose and special applications, saving manpower, short equipment training cycle
- More comprehensive, more advanced, and efficient automation functions, greatly reducing production costs and labor costs
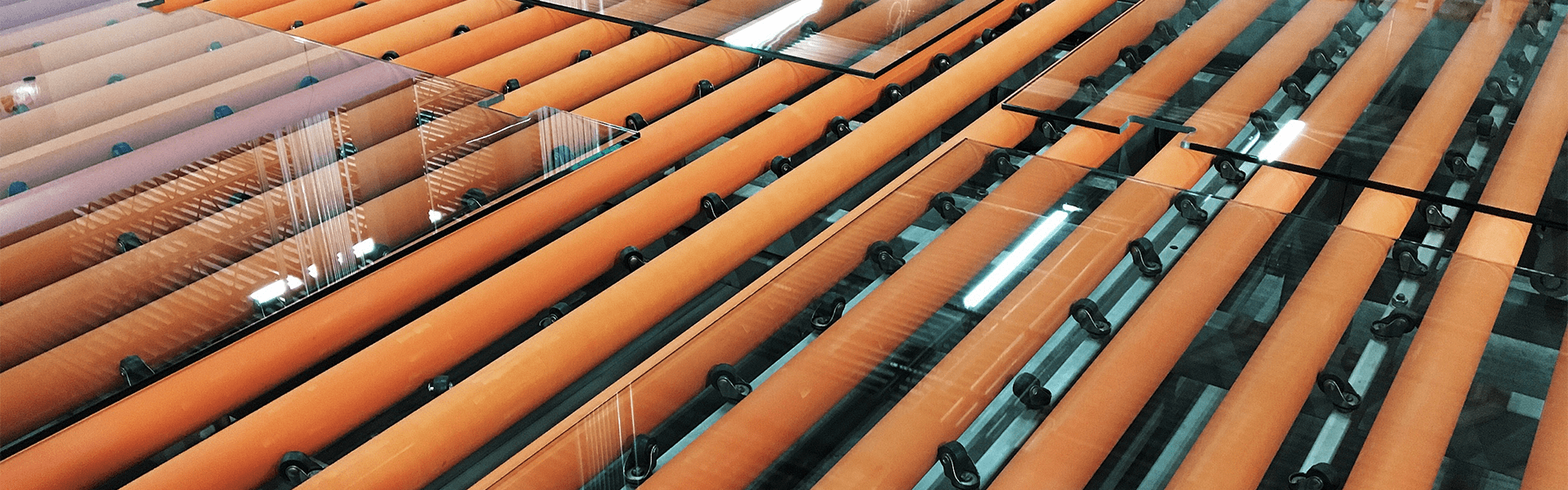
Machine Introduction
Non-Molding Series:
This bending tempering furnace is mainly used to produce curved tempered glass for construction, commercial curved tempered glass, food display cabinets, curved glass for high-end buses, as well as large quantities of single-curved and thin tempered glass for the home appliance and electric appliance industry, and glass for other purposes.
The shaped bending tempering furnace is mainly composed of seven parts: the loading section, the heating section, the forming quenching section, the unloading section, the blower system, and the electric control system. In the production of bent glass, the glass enters the furnace from the loading table and is heated in the heating section. After reaching a certain temperature, the glass is quickly discharged from the furnace, enters the roller table of the forming quenching section, is formed, strengthened, and is tempered before being discharged to the unloading table for unloading. With the new arc-forming system and flexible arc-changing mechanism, not only the arc shape is flexible and changeable, but also the arc is automatically changed. A variety of advanced devices facilitate accurate arc adjustment. The shaped air grid can be customized according to the shape of the glass to ensure the uniformity and consistency of the tempering stress. Servo system and hydraulic system control ensure high precision of glass shaping. The machine can automatically record different arc adjustment parameters, which can save time and effort in the production process. A number of advanced processes and technologies ensure the high quality of the glass surface. The features of the shaped bending tempering furnace are: the machine structure is complicated, but the operation is relatively simple. The product quality is high and stable, the equipment is reliable, the output is large, and the production cost is low.
Molding Series:
This shaped bending tempering furnace is specially designed for processing special-shaped curved tempered glass and is mainly used for curved tempered glass that is difficult to process in a large-scale roller bending tempering furnace. Its characteristics are low investment, good results, low power consumption, and few glass surface defects.
The working principle of this bending tempering furnace is that the glass and mold are placed on a special trolley, and they are driven into the furnace for gradual heating (local heating is used after a certain period of time). The heating of the mold compensates for the heat loss of the glass. When the glass reaches the softening temperature, it will be formed with the mold due to its weight or adsorption, and then it will be out of the furnace and enter the quenching section for strengthening cooling. At the same time, another piece of glass followed up and heated and tempered in the furnace in the same way. The tempered glass is taken off, and the trolley returns to the entrance along the track outside the furnace to load the pieces, waiting for the second entry into the furnace, this cycle is carried out. The heating section works continuously with high efficiency. A double-mold trolley or multiple trolleys can shorten the processing time of the glass, which is beneficial to increase the output. The mold is simple to manufacture, quick and convenient to replace, and the high-quality materials are not easy to deform, and the glass is formed and shaped accurately.